Worm Gear Motor Supplier
We design and manufacture AC and DC worm gear motors in a wide range of sizes. Whether it is high torque transmission, compact design or self-locking ability, we can provide unmatched motor solutions for your equipment.
In addition to standard gear worm motor, we can also provide you with customized alternatives:
- Shaft Configuration: Single or dual output shaft
- Mounting Options: Flange or base mount configuration
- Gear Ratio Selection: Gear ratio variations
- Enclosure Rating: Choose from different IP ratings for different environmental conditions.
- Accessories: Encoder, brake or thermal protector
Home / Worm Gear Motor
Structure
Knowing the worm drive motor’s construction guarantees lifespan and best performance when choosing the appropriate motor for a certain application.
Electric Motor
- Can be a DC (brushed/brushless) or AC (single/three-phase) motor.
- Converts electrical energy to mechanical, rotating the worm gear.
Worm
- An apparatus shaped like a screw.
- Engages the worm wheel, causing it to rotate and transmit motion and power.
Worm Wheel (Gear)
- A gear similar to a spur gear, meshing perpendicularly with the worm.
- Reduces speed & increases torque to the output shaft upon receiving motion from the worm.
Output Shaft
- Joined with the worm wheel.
- Delivers the reduced speed and increased torque to the connected load or mechanism.
Housing
- Usually composed of cast iron or aluminum.
- Protects components, supports structure, and aids heat dissipation.
Bearings
- Support the motor shaft, worm & output shaft.
- Reduce friction and wear, ensuring smooth rotation of the shafts.
Lubrication
- Grease or oil, depending on the design.
- Reduces friction, enhances efficiency, and prolongs component life.
Seals and Gaskets
- keeps lubricant inside the housing and stops the entry of dust, grime, and moisture.
By Types
Worm gear motors come in a variety of varieties, each designed to meet certain requirements and uses.
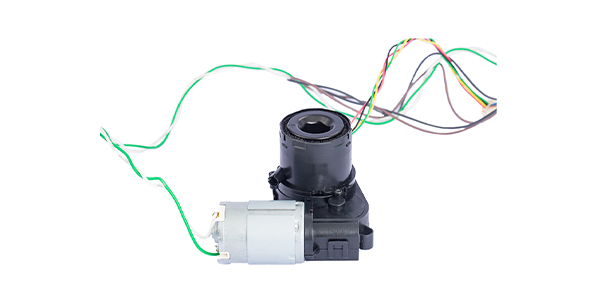
Brushed
- The Brushed Worm Gear Motor offers 1-50 Nm torque, 10-300 RPM speed, 50%-75% efficiency, and weighs 1-10kg with a 50-150mm diameter. Brushes and a commutator control current.
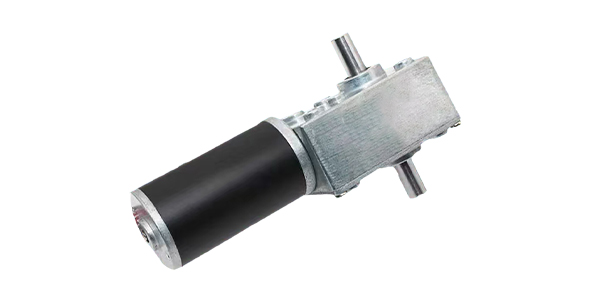
Brushless
- The Brushless Worm Gear Motor offers 2-100 Nm torque, 20-500 RPM velocity, 80-90% efficiency, with diameters of 60-180mm, weighing 1.5-12kg, and uses electronic commutation with permanent magnets.
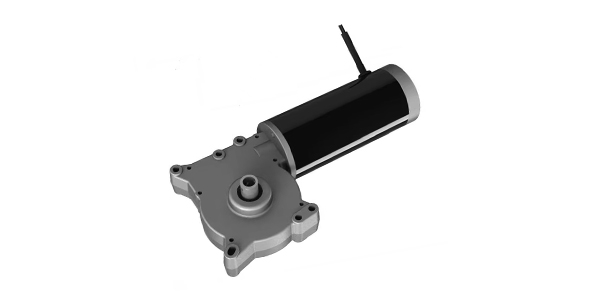
Stepper
- The Stepper Worm Gear Motor offers 0.5-30 Nm torque, 1-200 RPM speed, 30%-60% efficiency, and precise control in stages, with diameters from 40mm to 120mm and weights from 0.8KG to 8KG.
From 0 to N - Full Motor Solutions
By Current
DC Worm Gear Motor
- Power Source: Operates on direct current (DC) power, typically from batteries or DC power supplies (12V, 24V, 48V, etc.).
- Control: Easy to control speed and direction through voltage variation or pulse-width modulation (PWM).
- Torque: Generally provides high starting torque.
- Maintenance: Worm drive DC motor requires regular maintenance, especially for brushed DC motors which need brush replacement.
AC Worm Gear Motor
- Power Source: Operates on alternating current (AC) power, typically from the mains supply (110V, 220V, etc.).
- Control: Requires more complex control systems like variable frequency drives (VFD) to adjust speed.
- Torque: Provides consistent torque, suitable for continuous operation.
- Upkeep: In general, less upkeep is required than with brushed DC motors.
By Combination
Helical-Worm Gear Motors
- Design: Worm and helical gear combination.
- Efficiency: 70-85%
- Applications: Quiet, efficient applications like conveyors and packaging.
Bevel-Worm Gear Motors
- Design: Combination of bevel gears and worm gears.
- Efficiency: 50-70%
- Applications: High-torque, low-speed uses like material handling.
Planetary-Worm Gear Motors
- Design: Integrates planetary and worm gear systems.
- Efficiency: 80-90%
- Applications: Robotics, automation, and space-limited, high-torque applications.
Helical-Bevel-Worm Gear Motors
- Design: Combines helical, bevel, and worm gears.
- Efficiency: 60-80%
- Applications: Heavy-duty, reliable, and efficient applications like mining and industry.
Spur-Worm Gear Motors
- Design: Combination of spur gears and worm gears.
- Efficiency: 50-70%
- Applications: Low-cost, non-critical efficiency applications like simple machinery.
By Voltage
We provide worm drive gear motors with different voltage values. The 12V and 24V models are the most often used.
Parameters | 12v | 24v |
Voltage | 12V DC | 24V DC |
Rated Power | 50W | 100W |
Output Speed | 60 RPM | 50 RPM |
Torque | 20 Nm | 30 Nm |
Gear Ratio | 30:1 | 40:1 |
Efficiency | 60% | 65% |
High Torque Output | Worm gear motor 12v fits for applications requiring a lot of force. | Worm gear motor 24v provides significant torque, ideal for high-force applications. |
Applications
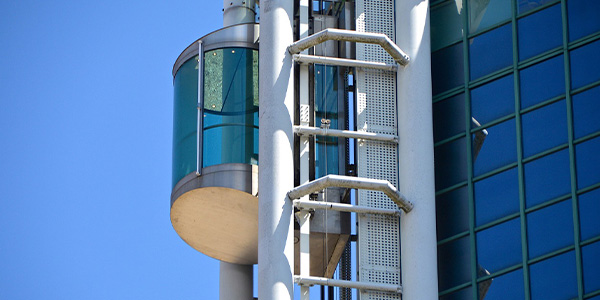
Elevators and Lifts
- Provides torque and control for smooth vertical movement, handling passengers and cargo. The self-locking function prevents free fall during power or mechanical failure, ensuring safety.
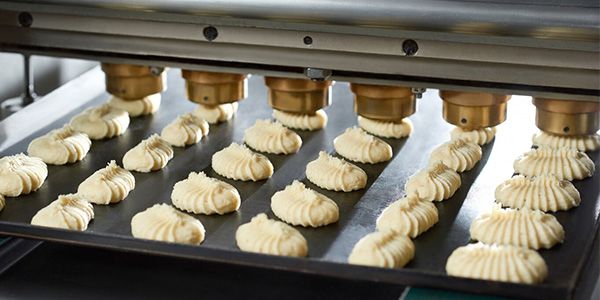
Food Processing Equipment
- Worm gear motors power mixers, grinders, conveyors, and packaging machines, providing torque and precise control for efficient, reliable food processing.
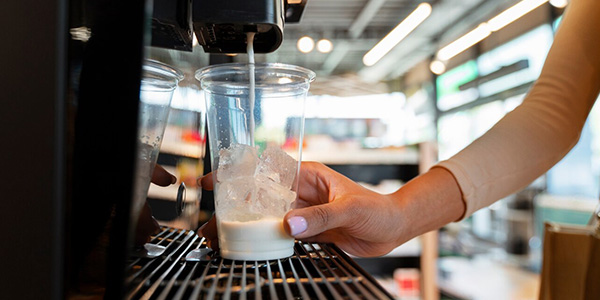
Beverage Dispensing Systems
- Worm drive electric motors drive pumps and dispensers in beverage machines, fitting into limited spaces to ensure smooth, accurate dispensing with consistent flow rates and portion sizes.
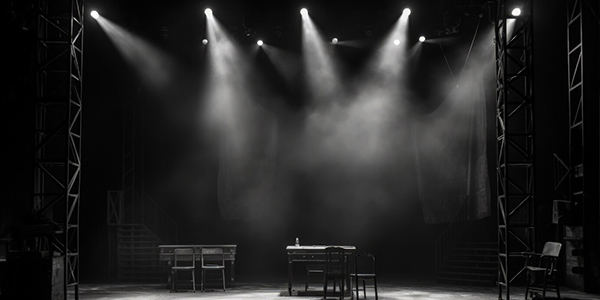
Stage Lifts
- Worm drive gear motor power stage lifts, mobile stages, platforms, and props in theaters and concert venues, meeting the demands of live performances.
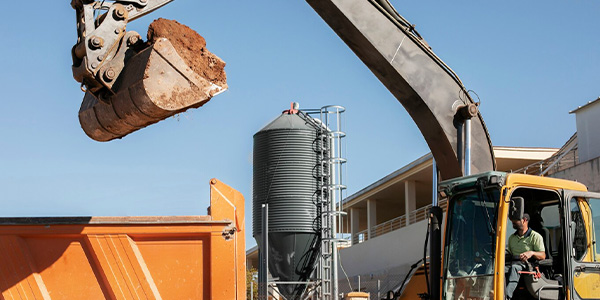
Concrete Mixers
- The motor powers the concrete mixer's drum, ensuring thorough mixing with necessary torque and speed. Reliable operation guarantees a uniform mix, crucial for concrete quality.
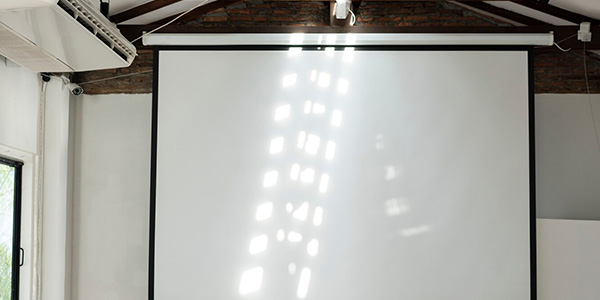
Projector Lifts
- Providing precise height control and stability, the self-locking feature prevents shifting. Smooth, quiet operation ensures a professional, distraction-free environment.
FAQ
What effect does a worm gear motor's gear ratio have on its operation?
A higher gear ratio increases torque and reduces speed, ideal for high-torque, precise control applications. Reduced gear ratios result in more speed but reduced torque.
What is the function of the worm motor gear in a worm gear motor?
The worm motor gear transmits power from the motor to the worm wheel, reducing speed and increasing torque for efficient and precise motion control.
What distinguishes a helical worm gear motor from other gear motor types?
A helical worm gear motor combines efficient helical gears with self-locking worm gears for smooth, quiet operation and high torque, ideal for precise positioning and high reduction ratios.
How does a high torque worm gear motor benefit industrial applications?
A high torque worm gear motor ensures robust power transmission and reliability, ideal for heavy-duty industrial machinery and automation systems requiring strong torque and precise control.